What is Receiving in the Context of the Fulfillment Process?
Common Steps in the Receiving Process
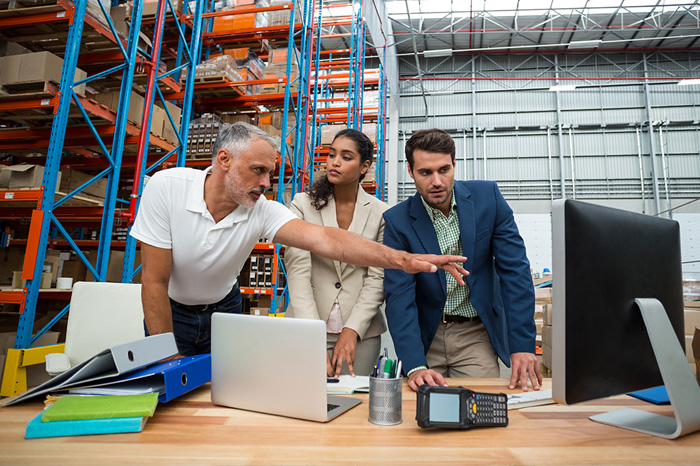
Unloading: Upon arrival, the goods are unloaded from trucks, containers, or other transport vehicles. This may involve the use of equipment such as forklifts, pallet jacks, or conveyor systems to move the items from the delivery vehicle to the receiving area.
Inspection: The received goods are visually inspected to ensure they match the details provided in the order to make sure the right products were delivered. Inspection also involves checking for any signs of damage, defects, or other issues between the delivered items and the order.
Counting and Verification: Each item is counted to confirm that the quantity matches the expected quantity specified in the purchase order. This step ensures accurate inventory records and helps identify any potential discrepancies or errors.
Documentation: The receiving process involves generating and updating various documents, including receiving reports or receiving slips. These documents capture relevant information such as the supplier details, item descriptions, quantities received, and any observations related to the condition of the goods.
Labeling and Identification: Received items may be labeled or tagged with appropriate identification, such as barcodes or RFID tags, to facilitate efficient tracking and inventory management within the warehouse.
Quality Control: In some cases, quality checks or sampling may be conducted during the receiving process to ensure that the received goods meet the specified quality standards. This is particularly important for industries with strict quality requirements, such as food, pharmaceuticals, or electronics.
Storage Allocation: Once the receiving process is complete, the goods are typically assigned a designated storage location within the warehouse. This ensures that the items are organized and can be easily located when needed for subsequent processes such as picking, packing, or order fulfillment.
Efficient and accurate receiving operations are crucial for maintaining inventory integrity, minimizing stock discrepancies, and enabling smooth material flow within the supply chain.